Categories
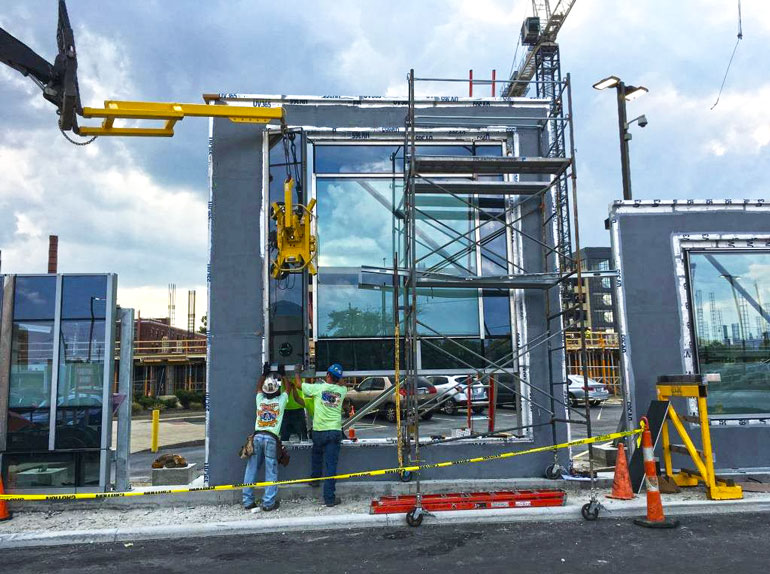
The Last Line of Defense: Building Envelope Design Implementation & Testing
By Bob Medziuch, AIA, ACHA, CCS
In previous posts, we’ve talked about the importance of the building envelope and some of the tools and methods used during the design process that the project team can implement. The final piece of the puzzle is to construct the envelope and follow through on the design. Some of the issues related to failures with the building envelope during the construction phase can be attributed to breakdowns in communication, lack of coordination with the design documents and unsuccessful follow-through on identified deficiencies. There are several methods, including submittals and mockups, that can be used to circumvent potential building enclosure concerns during construction. As we’ve discussed before, the cost of preventing and/or remedying issues will be much less now than after the building has been completed.
Submittals
The first step in implementing the design is the preparation of comprehensive submittal information related to the envelope. Each sub-contractor must submit the specified product data, installation instructions and other detailed information related to the materials specified and detailed. This is the first step in making sure the design is properly communicated with the construction team and should not be taken lightly. Deficiencies we typically see include incomplete submittals and product substitutions. The construction manager or general contractor has the first, and probably most crucial, opportunity to catch these deficiencies prior to submission to the design team.
It is equally important for the construction manager or general contractor to coordinate the various subcontractors’ work related to the envelope to ensure no work scope gaps exist. With today’s complex envelope systems, it is important that the work sequence is coordinated and understood by all the subcontractors. Construction tolerances between systems and material compatibility at transitions can be impacted by a lack of coordination between the subcontractors.
Another issue to be aware of is the timing of the submittals relative to the overall schedule. The submittals must be supplied well in advance of actual construction and should be timed to allow for the mockup wall to be constructed and evaluated several weeks prior to the final envelope construction on the building. This is critical to the envelope construction process.
Mockups
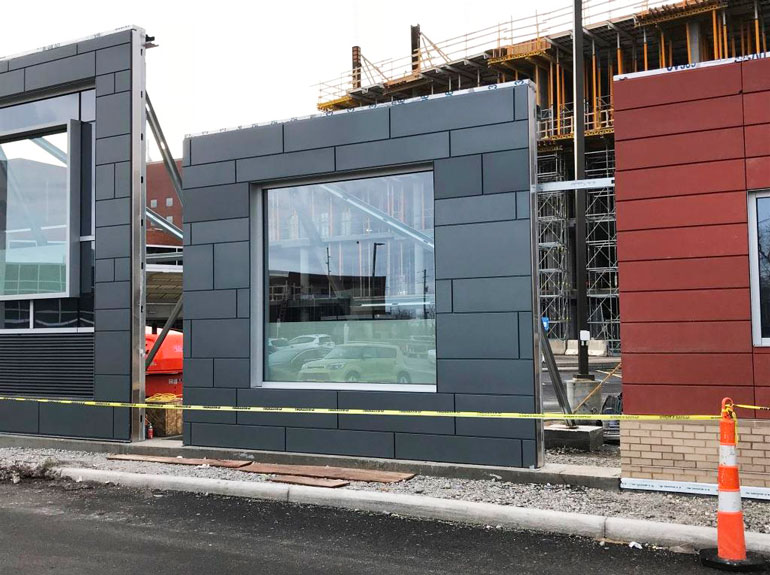
Once the submittal process is complete, the mockup can be constructed to allow the team to identify any constructability issues. The best approach is to require a preconstruction meeting with all the contractors who will be involved in the mockup construction process to review the relevant details and confirm that the approved submittals are being utilized.
An important factor is to require each of the lead subcontractors who will be involved in the actual construction of the building to be responsible for the construction on the mockup. When the team constructing the mockup is not the same team constructing the envelope on the building, information can be lost in translation or simply not communicated.
Mockups allow the identification of any constructability issues relative to the design so they can be addressed prior to actual envelope construction. At this point, details may need to be modified due to aesthetics, ease of construction, and cost savings.
Quality control testing is another benefit of utilizing building envelope mockups. After any constructability issues are resolved and implemented, the actual performance of the wall can be tested using several methods depending on the criteria being evaluated. Air and water infiltration are typically the two most important conditions that are evaluated. These tests are typically performed by third-party, independent testing consultants. An important part of this process is specifying the proper test and understanding the results. Clear expectations must be established prior to the testing so misunderstandings do not occur when the tests are complete.
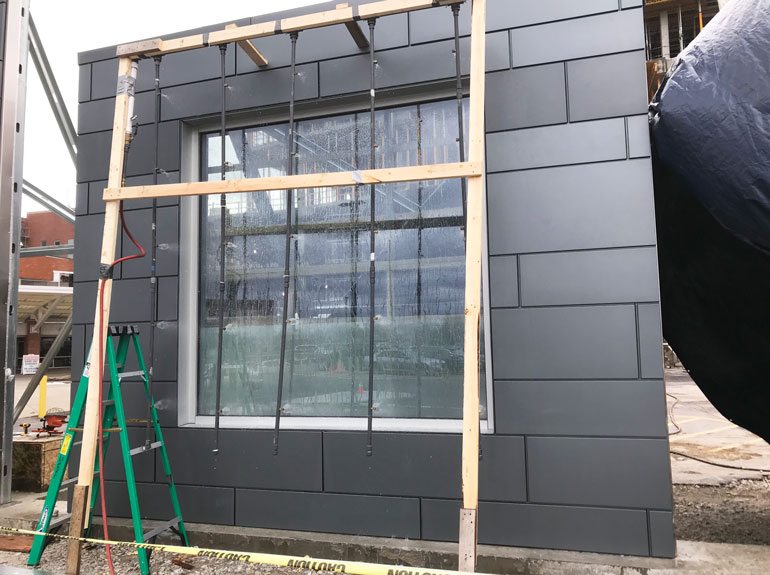
If the tests do result in a failure, the team must identify the cause and correct the deficiency. The deficiency could be related to a design issue, product failure or installation flaw. Once the deficiencies are corrected, it is important to communicate all changes to the construction team so work on the actual building will be done correctly. Additional testing can be performed on in-place construction, but it is more beneficial to all parties involved to rectify any issues prior to construction.
Early involvement and a solid plan, in combination with the tools and methods we’ve discussed for design and construction, will make the difference in ensuring a quality building envelope. The real key to success is clear communication among all relevant parties, as well as following through on a timely plan in the proper sequence. Avoid taking shortcuts to save time – they will cost you later!